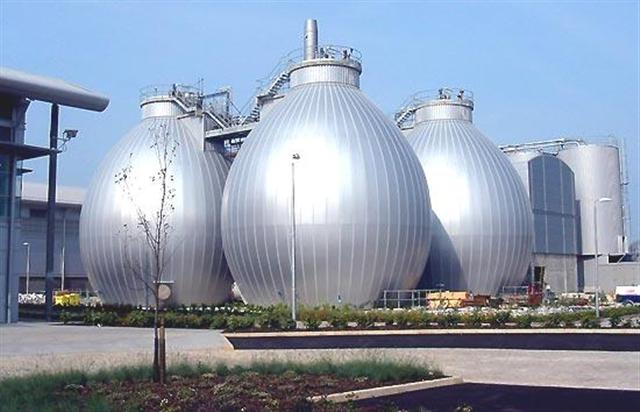
Anaerobic digestion (AD) is a natural process that occurs in swamps, peat bogs, even landfills. It is a series of process whereby micro-organisms mainly bacteria breaks down organic or biodegradable material in the absence of oxygen (anaerobic) to produce bio-gas - a mixture of of gases mostly methane and carbon dioxide, with a small amount hydrogen and trace hydrogen sulfide and a stabilized residue know as digestate.
The Environmental Permitting Regulation (England and Wales) (Amendment) Regulation 2012 defines Anaerobic Digestion to mean the mesophilic and thermophilic biological decomposition and stabilization of biodegradable material which-
is carried on under controlled anaerobic conditions
produces a methane-rich gas mixture, and
results in stable sanitized material that can be applied to land for the benefit of agriculture or to improve the soil structure or nutrients in land.
AD has been adapted by the waste industry in the treatment of organic wastes including organic industrial wastes (food processing for example) and the biodegradable portion of source-segregated or mechanically separated MSW. Anaerobic digestion is also widely used as a source of renewable energy. With increased focus on climate change mitigation, the re-use of waste as a resource and new technological approaches which have lowered capital costs, anaerobic digestion has in recent years received increased attention among governments in a number of countries, among these the United Kingdom, Germany and Denmark. The process produces a bio-gas, consisting of methane, carbon dioxide and other traces gases. This bio-gas can be used directly as cooking fuel, in combined heat and power gas engines or upgraded to natural gas-quality biomethane. The use of bio-gas as a fuel helps to replace fossil fuels. So where the bio-gas and digestates are utilized, i.e. the bio-gas is burnt to generate power and the digestate is applied to land improve soil structure, then AD can be said to be both a waste recovery and recycling operation.
AD chemistry and biology
The process that takes place in an Anaerobic digester is similar to that in a landfill, hence it's description as a controlled landfill reactor. The same processes occur except for the initial aerobic stage in a landfill. In AD, the aerobic stage is deliberately and completely excluded. Any aerobic treatment of the final digestate produced takes place outside the AD reactor.
There are four key biological and chemical stages of anaerobic digestion:
Hydrolysis
Acidogenesis
Acetogenesis
Methanogenesis
The digestion process begins with bacterial hydrolysis of the input materials to break down insoluble organic polymers, such as carbohydrates, and make them available for other bacteria. The enzyme produced by the bacteria breaks down the cellulose, lipids and proteins into simple sugars, fatty acids and amino acids respectively.
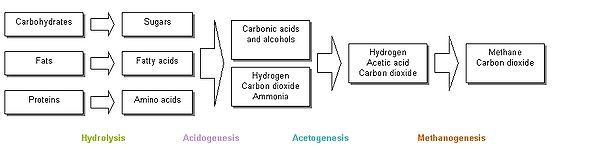
The key process stages of anaerobic digestion
Acidogenic bacteria further converts the sugars and amino acids into carbon dioxide, hydrogen, ammonia, and organic acids. The biological process of acidogenesis results in further breakdown of the remaining components by acidogenic (fermentative) bacteria. The process of acidogenesis is similar to the way milk sours. The gas produced during this phase typically contains 80% methane and 20% hydrogen. Acetogenic bacteria then convert these resulting organic acids into acetic acid, along with additional ammonia, hydrogen, and carbon dioxide. At the same time, other bacterial communities convert more complex carbohydrates directly into acetic acid. Finally, methanogens convert these products, mainly the acetic acid to methane and carbon dioxide. The methanogens are very active during this phase and they further convert carbon dioxide and hydrogen (generated during the hydrolysis of lipids) to generate more methane. The final gas composition is made up of approximately 66% methane and 33% carbon dioxide. Methanogenesis is sensitive to both high and low pHs and occurs between pH 6.5 and pH 8. The remaining, indigestible material the microbes cannot use and any dead bacterial remains constitute the digestate. A simplified generic chemical equation for the overall processes outlined above is as follows:

AD Technology
The digester is designed to reproduce the conditions in a landfill (excluding initial aerobic phase) but over a shorter period of time (two to four weeks). The feed-stock is mixed with water and the resultant slurry is fed into the reactor where it is stirred continuously to ensure good mixing. The feed-stock is also heated to maintain optimum temperature. As material is added to the reactor, an equivalent volume is removed. Any gas formed is collected at the top of the reactor and is withdrawn for storage. The gas is usually burnt on-site in a gas engine to generate power. Heat can also be recovered (to heat the feed-stock) from the exhaust gas of the engine used to burn the gas. This is discussed later.
Configuration
Anaerobic digesters can be operated using a number of different process configurations:
Batch or continuous
Temperature: Mesophilic or thermophilic
Solids content: High solids or low solids
Complexity: Single stage or multistage
Batch or continuous
Anaerobic digestion can be performed as a batch process or a continuous process.
In a batch system biomass is added to the reactor at the start of the process. The reactor is then sealed for the duration of the process.
To start the anaerobic digestion process, the batch processing mixed with already processed material. In a typical scenario, bio-gas production will be formed with a normal distribution pattern over time. Operator can use this fact to determine when they believe the process of digestion of the organic matter has completed. There is a risk of odor generation if a batch reactor is opened and emptied before the process is well completed.
A more advanced type of batch approach has limited the odor issues by integrating anaerobic digestion with in-vessel composting. In this approach inoculation takes place through the use of recirculated degasified percolate whereby excess water from a digestate is removed and returned to the reactor. After anaerobic digestion has completed, the biomass is kept in the reactor which is then used for in-vessel composting before it is opened. As the batch digestion is simple and requires less equipment and lower levels of design work, it is typically a cheaper form of digestion. Using more than one batch reactor at a plant can ensure constant production of bio-gas.
In continuous digestion processes, organic matter is constantly added (continuous complete mixed) or added in stages to the reactor (continuous plug flow; first in – first out). Here, the end products are constantly or periodically removed, resulting in constant production of bio-gas. A single or multiple digesters in sequence may be used. Examples of this form of anaerobic digestion include continuous stirred-tank reactors, upflow anaerobic sludge blankets, expanded granular sludge beds and internal circulation reactors.
Temperature
The two conventional operational temperature levels for anaerobic digesters are determined by the species of methanogens in the digesters:
Mesophilic digestion takes place optimally around 30 to 38 °C, or at ambient temperatures between 20 and 45 °C, where mesophiles are the primary microorganism present.
Thermophilic digestion takes place optimally around 49 to 57 °C, or at elevated temperatures up to 70 °C, where thermophiles are the primary microorganisms present.
Mesophilic species outnumber thermophiles, and they are also more tolerant to changes in environmental conditions than thermophiles. Mesophilic systems are, therefore, considered to be more stable than thermophilic digestion systems.
Though thermophilic digestion systems are considered to be less stable and the energy input is higher, more energy is removed from the organic matter. The increased temperatures facilitate faster reaction rates and, hence, faster gas yields. Higher temperatures also facilitates greater sterilization of the end digestate. This is an added benefit in countries where legislation, such as the Animal By-Products Regulations in the European Union, which requires end products to meet certain levels of reduction in the amount of bacteria in the output material.
Certain processes shred the waste finely and use a thermal pretreatment stage (hygienisation) to significantly enhance the gas output of the following standard mesophilic stage. The hygienisation process is also applied to reduce the pathogenic micro-organisms in the feed-stock. A drawback of operating at thermophilic temperatures is that more heat energy input is required to achieve the correct operational temperatures, which may not be outweighed by the increase in the outputs of bio-gas from the systems. Therefore, it is important to consider an energy balance for these systems.
Solids content
There are three different operational parameters associated with the solids content of the feed-stock to the digesters:
High solids (dry—stackable substrate)
High solids (wet—pumpable substrate)
Low solids (wet—pumpable substrate)
High solids (dry) digesters are designed to process materials with a solids content between 25 and 40%. Unlike wet digesters that process pumpable slurries, high solids (dry – stackable substrate) digesters are designed to process solid substrates without the addition of water. The primary styles of dry digesters are continuous vertical plug flow and batch tunnel horizontal digesters. Continuous vertical plug flow digesters are upright, cylindrical tanks where feed-stock is continuously fed into the top of the digester, and flows downward by gravity during digestion. In batch tunnel digesters, the feed-stock is deposited in tunnel-like chambers with a gas-tight door. Neither approach has mixing inside the digester. The amount of pretreatment, such as contaminant removal, depends both upon the nature of the waste streams being processed and the desired quality of the digestate. Size reduction is beneficial in continuous vertical systems, as it accelerates digestion, while batch systems avoid size reduction and instead require structure (e.g. yard waste) to reduce compaction of the stacked pile. Continuous vertical dry digesters have a smaller footprint due to the shorter effective retention time and vertical design.
Wet digesters can be designed to operate in either a high-solids content, with a total suspended solids (TSS) concentration greater than ~20%, or a low-solids concentration less than ~15%.
High solids (wet) digesters process a thick slurry that requires more energy input to move and process the feed-stock. The thickness of the material may also lead to associated problems with abrasion. Unlike low solids, high solid digesters will typically have a lower land requirement due to the lower volumes associated with the moisture.
Low solids (wet) digesters can transport material through the system using standard pumps that require significantly lower energy input. Low solids digesters require a larger amount of land than high solids due to the increased volumes associated with the increased liquid-to-feedstock ratio of the digesters. There are benefits associated with operation in a liquid environment, as it enables more thorough circulation of materials and contact between the bacteria and their food. This enables the bacteria to more readily access the substances on which they are feeding, and increases the rate of gas production.
Complexity
There are two main configuration complexities: Single and Double-Stage Digestion Systems.
A singe-stage digestion system requires a single, sealed reactor or holding tank in which all of the biological reactions occur. Using a single stage reduces construction costs, but results in less control of the reactions occurring within the system. Acidogenic bacteria, through the production of acids, reduce the pH of the tank. As Methanogenic bacteria require stable pH, the biological reactions of the different species in a single-stage reactor can be in direct competition with each other. Another one-stage reaction system is an anaerobic lagoon. These lagoons are pond-like, earthen basins used for the treatment and long-term storage of manures. Here the anaerobic reactions are contained within the natural anaerobic sludge contained in the pool. Odour may be an issue unless the lagoons are properly fitted with covers.
A two-stage digestion system (multistage) has different digestion vessels which are optimised to bring maximum control over the bacterial communities (mainly acidogenic and methanogenic bacterias) living within the digesters. Acidogenic bacteria produce organic acids (thereby affecting pH) and grow and reproduce quicker than methanogenic bacteria. Methanogens require stable pH and temperature to optimise their performance.
Under typical circumstances, hydrolysis, acetogenesis, and acidogenesis occur within the first reaction vessel. The organic material is then heated to the required operational temperature (either mesophilic or thermophilic) prior to being pumped into a methanogenic reactor. The initial hydrolysis or acidogenesis tanks prior to the methanogenic reactor can provide a buffer to the rate at which feedstock is added. Some processes employ pasteurisation or sterilisation stage prior to digestion or between the two digestion tanks to kill harmful bacteria in the input waste. Notably, it is not possible to completely isolate the different reaction phases, and often some biogas is produced in the hydrolysis or acidogenesis tanks.
Residence time
The residence time in a digester varies with the amount and type of feed material, the configuration of the digestion system, and whether it be one-stage or two-stage.
In the case of single-stage thermophilic digestion, residence times may be in the region of 14 days, which, compared to mesophilic digestion, is relatively fast. The plug-flow nature of some of these systems will mean the full degradation of the material may not have been realized in this timescale. In this event, digestate exiting the system will be darker in colour and will typically have more odor. In two-stage mesophilic digestion, residence time may vary between 15 and 40 days.
Feed-stock
The most important initial issue when considering the application of anaerobic digestion systems is the feed-stock to the process. Almost any organic material can be processed with anaerobic digestion; however, if bio-gas production is the aim, the level of putrescibility is the key factor in its successful application. The more digestible the material, the higher the gas yields possible from the system.
Feed-stocks can include biodegradable waste materials, such as waste paper, grass clippings, leftover food, sewage, and animal waste. Woody wastes are the exception, because they are largely unaffected by digestion, as most anaerobes are unable to degrade lignin. Xylophalgeous anaerobes (lignin consumers) or using high temperature pretreatment, such as pyrolysis, can be used to break down the lignin. Anaerobic digesters can also be fed with specially grown energy crops, such as silage, for dedicated bio-gas production. In Germany and continental Europe, these facilities are referred to as "bio-gas" plants.
Anaerobes can break down material with varying degrees of success from readily, in the case of short-chain hydrocarbons such as sugars, to over longer periods of time, in the case of cellulose. Anaerobic microorganisms are unable to break down long-chain woody molecules, such as lignin.
Anaerobic digesters were originally designed for operation using sewage sludge and manures. Sewage and manure are not, however, the material with the most potential for anaerobic digestion, as the biodegradable material has already had much of the energy content taken out by the animals that produced it. Therefore, many digesters operate with co-digestion of two or more types of feed-stock. For example, in a farm-based digester that uses dairy manure as the primary feed-stock, the gas production may be significantly increased by adding a second feed-stock, e.g., grass and corn (typical on-farm feed-stock), or various organic byproducts, such as slaughterhouse waste, fats, oils and grease from restaurants, organic household waste, etc.

Digesters processing dedicated energy crops can achieve high levels of degradation and bio-gas production. Slurry-only systems are generally cheaper, but generate far less energy than those using crops, such as maize and grass silage; by using a modest amount of crop material (30%), an anaerobic digestion plant can increase energy output tenfold for only three times the capital cost, relative to a slurry-only system.
Substrate composition
Substrate composition is a major factor in determining the methane yield and methane production rates from the digestion of biomass. Techniques to determine the compositional characteristics of the feed-stock are available, while parameters such as solids, elemental, and organic analyses are important for digester design and operation.
Moisture content
A second consideration related to the feed-stock is moisture content. Dryer, stackable substrates, such as food and yard waste, are suitable for digestion in tunnel-like chambers. Tunnel-style systems typically have near-zero wastewater discharge, as well, so this style of system has advantages where the discharge of digester liquids are a liability. The wetter the material, the more suitable it will be to handling with standard pumps instead of energy-intensive concrete pumps and physical means of movement. Also, the wetter the material, the more volume and area it takes up relative to the levels of gas produced. The moisture content of the target feed-stock will also affect what type of system is applied to its treatment. To use a high-solids anaerobic digester for dilute feed-stocks, bulking agents, such as compost, should be applied to increase the solids content of the input material. Another key consideration is the carbon:nitrogen ratio of the input material. This ratio is the balance of food a microbe requires to grow; the optimal C:N ratio is 20–30:1. Excess N can lead to ammonia inhibition of digestion.
Contamination
Many components of MSW contain inorganic wastes which are not amenable to bio-degradation. Pre-treatment of the waste load is required to remove the inorganic or non biodegradable components. If it is not removed, then the digesters can be blocked and will not function efficiently. It is with this understanding that mechanical biological treatment plants are designed. Mechanical is obviously quicker but the digestate may contain unwanted contaminants including plastics, metals, glasses and in some cases heavy metal contaminants. In such cases, the digestate has to be disposed of to landfill which defeats the whole purpose (see legislative definition of AD above).
After sorting or screening to remove any physical contaminants from the feed-stock, the material is often shredded, minced, and mechanically or hydraulically pulped to increase the surface area available to microbes in the digesters and, hence, increase the speed of digestion. The maceration of solids can be achieved by using a chopper pump to transfer the feed-stock material into the airtight digester, where anaerobic treatment takes place.
Digestate Treatment
The digestate can not be used directly and requires further treatment before use or disposal. The excess water is removed and returned to the reactor. The remaining solid digestate is then cured in an aerobic process similar to composting processes. The cured digestate can then be used in the same way as compost. It should be noted that a quality protocol exists for anaerobic digestates - BSI PAS110 certification scheme. This is managed by the Environment Agency.
Power generation Bio-gas grid-injection is the injection of bio-gas into the natural gas grid. As an alternative, the electricity and the heat can be used for on-site generation, resulting in a reduction of losses in the transportation of energy. If localized anaerobic digestion facilities are embedded within an electrical distribution network, they can help reduce the electrical losses associated with transporting electricity over a national grid.
Methane and power produced in anaerobic digestion facilities can be used to replace energy derived from fossil fuels, and hence reduce emissions of greenhouse gases, because the carbon in biodegradable material is part of a carbon cycle. The carbon released into the atmosphere from the combustion of bio-gas has been removed by plants for them to grow in the recent past, usually within the last decade, but more typically within the last growing season. If the plants are regrown, taking the carbon out of the atmosphere once more, the system will be carbon neutral. In contrast, carbon in fossil fuels has been sequestered in the earth for many millions of years, the combustion of which increases the overall levels of carbon dioxide in the atmosphere.
Bio-gas from sewage works is sometimes used to run a gas engine to produce electrical power, some or all of which can be used to run the sewage works. Some waste heat from the engine is then used to heat the digester. The waste heat is, in general, enough to heat the digester to the required temperatures. The power potential from sewage works is limited – in the UK, there are about 80 MW total of such generation, with the potential to increase to 150 MW, which is insignificant compared to the average power demand in the UK of about 35,000 MW. The scope for bio-gas generation from non-sewage waste biological matter – energy crops, food waste, abattoir waste, etc. - is much higher, estimated to be capable of about 3,000 MW. Farm bio-gas plants using animal waste and energy crops are expected to contribute to reducing CO2 emissions and strengthen the grid, while providing UK farmers with additional revenues.
Some countries offer incentives in the form of, for example, feed-in tariffs for feeding electricity onto the power grid to subsidize green energy production.
Fertiliser and soil conditioner
The solid, fibrous component of the digested material can be used as a soil conditioner to increase the organic content of soils. Digester liquor can be used as a fertilizer to supply vital nutrients to soils instead of chemical fertilizers that require large amounts of energy to produce and transport. The use of manufactured fertilizers is, therefore, more carbon-intensive than the use of anaerobic digester liquor fertilizer.
Cooking gas
By using a bio-digester, which produces the bacteria required for decomposing, cooking gas is generated. The organic garbage like fallen leaves, kitchen waste, food waste etc. are fed into a crusher unit, where the mixture is conflated with a small amount of water. The mixture is then fed into the bio-digester, where the bacteria decomposes it to produce cooking gas. This gas is piped to kitchen stove. A 2 cubic meter bio-digester can produce 2 cubic meter of cooking gas. This is equivalent to 1 kg of LPG. The notable advantage of using a bio-digester is the sludge which is a rich organic manure.
Products
The three principal products of anaerobic digestion are biogas, digestate, and water.

Biogas
Bio-gas is the ultimate waste product of the bacteria feeding off the input biodegradable feed-stock (the methanogenesis stage of anaerobic digestion is performed by archaea - a micro-organism on a distinctly different branch of the phylogenetic tree of life to bacteria), and is mostly methane and carbon dioxide, with a small amount hydrogen and trace hydrogen sulfide. (As-produced, bio-gas also contains water vapor, with the fractional water vapor volume a function of bio-gas temperature). Most of the bio-gas is produced during the middle of the digestion, after the bacterial population has grown, and tapers off as the putrescible material is exhausted. The gas is normally stored on top of the digester in an inflatable gas bubble or extracted and stored next to the facility in a gas holder.
The methane in bio-gas can be burned to produce both heat and electricity, usually with a reciprocating engine or micro-turbine often in acogeneration arrangement where the electricity and waste heat generated are used to warm the digesters or to heat buildings. Excess electricity can be sold to suppliers or put into the local grid. Electricity produced by anaerobic digesters is considered to be renewable energy and may attract subsidies. Bio-gas does not contribute to increasing atmospheric carbon dioxide concentrations because the gas is not released directly into the atmosphere and the carbon dioxide comes from an organic source with a short carbon cycle. In countries such as Switzerland, Germany and Sweden, the methane in the bio-gas may be compressed for it to be used as a vehicle transportation fuel or input directly into the gas mains.
Bio-gas may require treatment or 'scrubbing' to refine it for use as a fuel. Hydrogen sulfide, a toxic product formed from sulfates in the feed-stock, is released as a trace component of the bio-gas. The Environment Agency puts strict limits on the emission of hydrogen sulfide, and, if the levels of hydrogen sulfide in the gas are high, gas scrubbing and cleaning equipment (such as amine gas treating) will be needed to process the bio-gas to within accepted levels. Alternatively, the addition of ferrous chloride FeCl2 to the digestion tanks inhibits hydrogen sulfide production.
Volatile siloxanes can also contaminate the bio-gas; such compounds are frequently found in household waste and wastewater. In digestion facilities accepting these materials as a component of the feed-stock, low-molecular-weight siloxanes volatilize into bio-gas. When this gas is combusted in a gas engine, turbine, or boiler, siloxanes are converted into silicon dioxide (SiO2), which deposits internally in the machine, increasing wear and tear. Practical and cost-effective technologies to remove siloxanes and other bio-gas contaminants are available at the present time. In certain applications, in situ treatment can be used to increase the methane purity by reducing the off-gas carbon dioxide content, purging the majority of it in a secondary reactor.
Digestate

Digestate is the solid remnants of the original input material to the digesters that the microbes cannot use. It also consists of the mineralised remains of the dead bacteria from within the digesters. Digestate can come in three forms: fibrous, liquor, or a sludge-based combination of the two fractions. In two-stage systems, different forms of digestate come from different digestion tanks. In single-stage digestion systems, the two fractions will be combined and, if desired, separated by further processing.
The second by-product (acidogenic digestate) is a stable, organic material consisting largely of lignin and cellulose, but also of a variety of mineral components in a matrix of dead bacterial cells; some plastic may be present. The material resembles domestic compost and can be used as such or to make low-grade building products, such as fiberboard. The solid digestate can also be used as feed-stock for ethanol production.
The third byproduct is a liquid (methanogenic digestate) rich in nutrients, which can be used as a fertilizer, depending on the quality of the material being digested. Levels of potentially toxic elements (PTEs) should be chemically assessed. This will depend upon the quality of the original feed-stock. In the case of most clean and source-separated biodegradable waste streams, the levels of PTEs will be low. In the case of wastes originating from industry, the levels of PTEs may be higher and will need to be taken into consideration
Digestate typically contains elements, such as lignin, that cannot be broken down by the anaerobic microorganisms. Also, the digestate may contain ammonia that is phytotoxic, and may hamper the growth of plants if it is used as a soil-improving material. For these two reasons, a maturation or composting stage may be employed after digestion. Lignin and other materials are available for degradation by aerobic microorganisms, such as fungi, helping reduce the overall volume of the material for transport. During this maturation, the ammonia will be oxidized into nitrates, improving the fertility of the material and making it more suitable as a soil improver. Large composting stages are typically used by dry anaerobic digestion technologies.
Wastewater
The final output from anaerobic digestion systems is water, which originates both from the moisture content of the original waste that was treated and water produced during the microbial reactions in the digestion systems. This water may be released from the dewatering of the digestate or may be implicitly separate from the digestate. In some sites, the excess water is removed and returned to the reactor as explained above.
The wastewater exiting the anaerobic digestion facility will typically have elevated levels of biochemical oxygen demand (BOD) and chemical oxygen demand (COD). These measures of the reactivity of the effluent indicate an ability to pollute. Some of this material is termed 'hard COD', meaning it cannot be accessed by the anaerobic bacteria for conversion into bio-gas. If this effluent were put directly into watercourses, it would negatively affect them by causing eutrophication. As such, further treatment of the wastewater is often required. This treatment will typically be an oxidation stage wherein air is passed through the water in a sequencing batch reactors or reverse osmosis unit.
Komentari